Over the next couple of weeks we’ll be running a series of 1:1 interviews with the KTE (Knowledge Transfer Experiment) teams that joined Better Factory through our second open call. These incredible teams are each made up of a SME, artist and technology provider, working together to develop new and personalized products, become cyber-physical systems, and transforming into Lean-agile production facilities.
The REFINE project aims to re-shore the design, production and innovation of scuba diving fins to SEACSUB, the manufacturer in Italy.
Their KTE team includes:
- SEASCUB (Manufacturing company)
- NMASA Design (Artist)
- Canonical Robots (Technology Provider)
Without further ado, let’s dive into the interview!
Hello, thank you for joining us! To start off, could you tell us why you decided to apply to Better Factory?
SME SEACSUB: We decided to be part of this project to keep on bringing back production from Asia, so why not take advantage of this opportunity to bring back the production of one of our best-selling fins, the F1. Plus, we have the chance to revamp it, make it better, and more competitive on the market. Italian production means better quality, production under control without logistic issues.
Artist NMASA Design: For the studio, the programme was a perfect opportunity to explore new sectors, experiment with new ideas, and work a bit outside of our comfort zone.
Tech provider Canonical Robots: We decided to apply to Better Factory because we believe that the rising market share of collaborative robotic solutions presents a significant opportunity. We are confident that the solution we plan to develop within ReFINe will be highly flexible and applicable to other SEAC products and to a wide range of other potential manufacturing realities.
“This experiment can set a precedent for the successful collaboration of technology, artistry, and manufacturing.”
Tech provider Canonical Robots:
Can you tell us more about the specific challenges you face in re-shoring the design and production of scuba diving fins?
SME SEACSUB: SEACSUB will face different challenges both in the reshoring design and in production of scuba diving fins. From the design side, SEACSUB will make a lighter product while maintaining the performance of the fins. SEACSUB wants to take advantage of the opportunity to customise production trying new materials and different colours combination.
From the production perspective SEACSUB wants to reduce the raw materials consumption and to reduce the molding phases. The reduction of the molding phases will decrease the energy absorbed by the molding machines. Within ReFINe, SEACSUB wants also to reduce the number of post-molding operations (i.e., burrs remotion) and the quantity of defective fins delivered to the customers; this will lead to a reduction of waste material and number of complaints. Another challenge that SEACSUB wants to address is the reduction in CO2 emissions, since we won’t move anymore F1 from Asia to Italy.
Artist NMASA Design: From us as a design studio with a big focus on handcrafts objects, the biggest challenge is to work in a context that is not familiar to us at all. Fins are pure industrialised products full of tiny details, lots of technical constraints, and a very specific design language that is quite homogeneous throughout the sector.
Tech provider Canonical Robots: In our role as Canonical Robots, the primary difficulty we face in bringing the fin production process back to Italy is incorporating digital twins and cooperative robots into SEAC’s current structure. It’s crucial that we meticulously strategise, experiment, and evaluate to guarantee the smooth functioning of our robotic systems in conjunction with human workers. The ultimate goal is to boost efficiency, reduce physical labor, and enhance the welfare of the workforce.
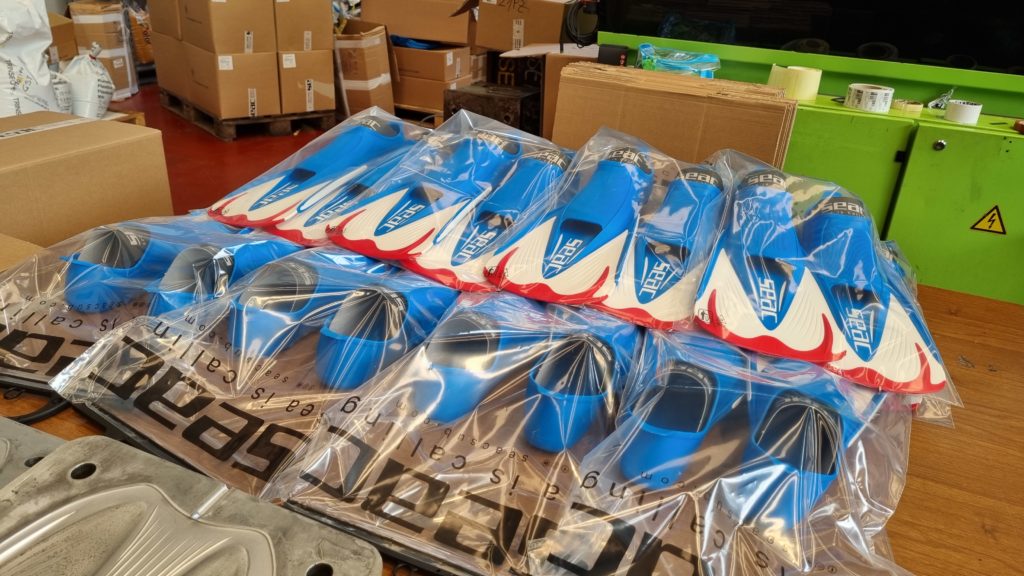
How do you expect the introduction of the collaborative robot into the factory will impact the production process?
SME SEACSUB: The wellness of our workers will improve thanks to the Cobot, which will address the most not ergonomic operations. Plus, the production process will be optimised thanks to the deployment of a digital twin solution.
Tech provider Canonical Robots: A robotic collaboration application will increase productivity and decrease and simplify strenuous activities for the operator. This collaborative robot will be located close to a moulding machine, carrying out the removal, the gripping operation of the moulded piece in the operator’s place and holding the pieces in a suitable position for the removal of the sprue and burrs. This change in the structure of the production cycle will be analysed through a simple digital twin to evaluate the waiting times for the operator and the robot in compliance with the moulding cycle times.
How do you expect that the artistic experimentation with NMASA Design will influence the design and functionality of the scuba diving fins?
Artist NMASA Design: In addition to the final optimisation work, NMASA design is expected to import visual codes and elements from other sectors as a way to explore alternative aesthetics for the new design. Furthermore, the design studio is expected to find effective ways to implement personalisation in the sector, which will lead to a future expansion of the product portfolio and personalisation options for SEAC customers.
Tech provider Canonical Robots: From Canonical Robots perspective, we anticipate that NMASA Design’s artistic experimentation will significantly enhance both the aesthetics and functionality of the scuba diving fins. NMASA’s innovative product design and mold optimisation approaches can lead to fins with improved customisability, enabling more variety in color, shape, and surface finish. As a tech provider, this requires us to ensure that our collaborative robots and digital twins can effectively accommodate and adapt to these varied designs without compromising on production efficiency or quality.
How will you work to reduce waste and increase sustainability in the manufacturing process?
SME SEACSUB: The diving sector highly relies on the conservation of the sea and its population. Indeed SEAC, during its several years of activity, has always kept a special eye on the environmental impact of its industrial activities. This has brought SEAC towards a more and more green approach, trying to optimise their production processes in terms of energy consumption and waste production.
Artist NMASA Design: Thanks to the optimised design of a lighter fin, 7% less raw material will be used. Considering non-renewable sources, this percentage will be reflected in CO2 emission reductions. Furthermore, the KTE is going to test different possibilities for reintroducing the production waste again in the production cycle, making the whole process more circular.
Tech provider Canonical Robots: Thanks to the human-robot collaboration, a machine usage optimisation will be achieved. This will be reflected in lower energy consumption by 10% on production cycles. Furthermore, thanks to the deployment of sophisticated measure control for the quality of the final product, a reduction of 15% of defective fin will be delivered to the final customer, decreasing the number of complaints to the company and then the discarded pieces.
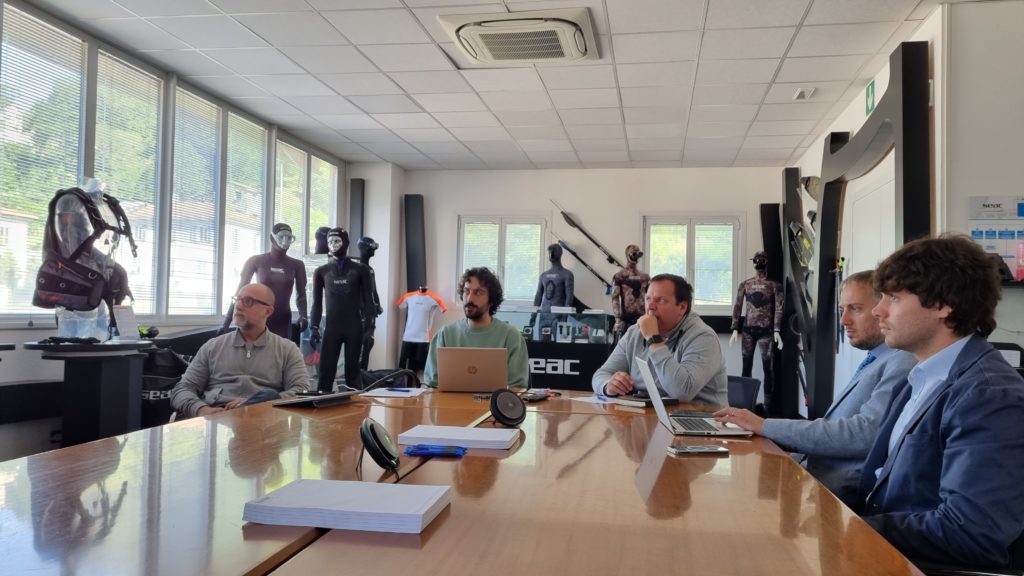
Can you tell us more about the use of digital twin technology to analyse the new production cycle configuration?
Tech provider Canonical Robots: Canonical Robots will contribute through the installation of a collaborative robot and the realisation of a simple digital twin to analyse the production cycle, to optimise the process and to relieve the operator from the most arduous work. The digital twin will allow the consortium to evaluate the impact of each collaboration scenario between the cobot and the operator, identifying the optimal one.
How do you foresee that this experiment might inform future collaborations between artists and manufacturers?
Tech provider Canonical Robots: This experiment can set a precedent for the successful collaboration of technology, artistry, and manufacturing. By demonstrating how NMASA Design’s product designs can be seamlessly integrated with our robotic and digital twin technologies, we can highlight the benefits of these interdisciplinary collaborations. This will lead to more customised, efficient, and sustainable production processes. Moreover, the success of this project could encourage more manufacturers to embrace such collaborations.
If you’d like to learn more about REFINE and their experiment, don’t forget you can check out their KTE page here!