Over the next couple of weeks we’ll be running a series of 1:1 interviews with the KTE (Knowledge Transfer Experiment) teams that joined Better Factory through our first open call. These incredible teams are each made up of a SME, artist and technology provider, working together to develop new and personalized products, become cyber-physical systems, and transforming into Lean-agile production facilities.
DSBSF are one of the KTE teams that joined us in our first Open Call, and are working on bringing weighing scale design and development into the 21st century.
The KTE focuses on implementing a new phygital scale design for sustainable, personalised and improved production, international expansion and local collaborations.
Their KTE team includes:
- Delmac Scales – Manufacturing company (Greece)
- Sara Alvarez Vinagre – Artist (Netherlands)
- NO Solutions Development d.o.o.- Technology supplier (Serbia)
So let’s jump into the interview!
Hello, thank you for joining us! Could you define the project in one short sentence?
Delmac Scales (Manufacturing company): The project will apply new technologies to create a more efficient scales factory.
Sara Alvarez Vinagre (Artist): The project is about creating a digital design for scales that enables easy customization, while also making them more sustainable using 3D printing, recycled plastic, and extended reality (XR) tools.
NO Solutions Development d.o.o (Tech provider): The project will develop new IT modules to improve scales production.
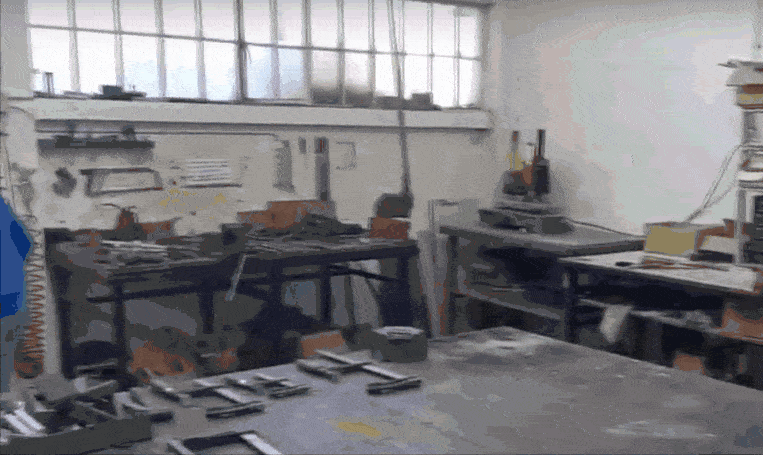
Why did you decide to apply to Better Factory?
Delmac Scales (Manufacturing company): We decided to apply because we strongly believe that Better Factory can help us improve our business in the digital era.
Sara Alvarez Vinagre (Artist): Coming from an engineering background, I really liked the idea of merging artistic and technical efforts in the same project to create innovative solutions.
NO Solutions Development d.o.o (Tech provider): We decided to apply because Better Factory is perfectly suited for the further development of our product.
How do you think Better Factory will help you?
Delmac Scales (Manufacturing company): We are expecting to enhance the product using new technologies, set up better customer support and use it as an opportunity to expand our market in other EU countries.
Sara Alvarez Vinagre (Artist): I expect to be challenged and pushed into areas out of my comfort zone, having to explore new topics or methods that I wouldn’t have thought of by myself. This will strengthen my practice and widen my perspective, as well as give me a great opportunity to showcase my abilities as a designer and maker.
NO Solutions Development d.o.o (Tech provider): With the help of Better Factory’s tools and financing, we will be able to continue developing the Voicing system and a new module for remote service with AG reality.
How would you position yourselves in the market taking into account your processes and final products?
Delmac Scales (Manufacturing company): We offer very high-quality products and a long-term relationship with clients, but the current manual customization process and lack of means to provide a remote service both restrict us in our current stage of development.
Why is it important to collaborate with local plastic waste recycling community in Athens?
Delmac Scales (Manufacturing company): Adding parts made from recycled plastic in our production will not only save costs, waste and energy, but also give a new identity to some of our products.
Nara Alvarez Vinagre (Artist): I believe that collaborating with the local plastic waste recycling community contributes to both the environmental and social sustainability of the SME’s products. What I mean by this is that it won’t only create a product that is produced with local materials and reincorporates waste in the production chain, but it will also nurture local networking, making the community more connected and resilient.
NO Solutions Development d.o.o (Tech provider): By being a valuable member in a project, which uses tech innovations to create eco-friendly solutions and raise awareness about the amount of plastic that is discarded by local communities in Athens, we are adding a green marketing eco label to our name.
What are the economical, technical and societal impacts of your project (main impact of each category)?
Delmac Scales (Manufacturing company) (economical): With a more efficient manufacturing cycle and logistics plan, we will reduce our production time. Cost reductions will be accomplished by saving energy saving, offering a remote service, having an automated customization process and using recycled plastic. Expanding to the EU market will also provide significant profits.
Sara Alvarez Vinagre (Artist): From an economic perspective, the product redesign and remote customer support will open up opportunities for new markets. On the technical side, having a fully digital and parametric design will reduce the time it takes to apply changes to the scale design and enable extended reality applications. On the societal topic, collaborating with local plastic recycling communities will strengthen the network of the SME and create a more connected and local manufacturing scenario.
NO Solutions Development d.o.o (Tech provider): For Delmac, both this project and the use of RAMP platform offer the ability to expand their customer base outside of Greece as well as enhance their production using new technologies, while providing online services to customers through Augmented Reality and IoT.
Since monitoring of the workers’ posture and fatigue will make work easier, it will certainly bring good feedback from workers.
NO Solutions Development d.o.o (Tech provider)
How do you think your employees will view this new way of working? And your customers?
Delmac Scales (Manufacturing company): Implementing AGV, Cognitive HRI and the monitoring of workers’ posture and fatigue will improve the day-to-day working conditions of our employees, provide new knowledge and maximize the efficiency of their skills with minimum effort. For our customers, the automated customization process will give them the opportunity to better visualize the end product while ordering and the remote service/maintenance feature will reduce the cost of the service, while also enabling faster repairing.
Sara Alvarez Vinagre (Artist): For the employees, as with any new process, it will probablytake some time to adjust to the changes, but I believe it will add tangible benefits that will make the effort worthwhile. For the customers I think the gain is quite significant, so I hope they will be excited about the possibilities that we are going to offer them with this project.
NO Solutions Development d.o.o (Tech provider): Since monitoring of the workers’ posture and fatigue will make work easier, it will certainly bring good feedback from workers. The adoption of new and interesting technology (AG reality) for faster and easier remote service/maintenance will certainly give positive comments from production and customers as well.
If you’d like to learn more about DSBSF and their experiment, don’t forget you can check out their KTE page here, including a cool video!