Over the next couple of weeks we’ll be running a series of 1:1 interviews with the KTE (Knowledge Transfer Experiment) teams that joined Better Factory through our first open call. These incredible teams are each made up of a SME, artist and technology provider, working together to develop new and personalized products, become cyber-physical systems, and transforming into Lean-agile production facilities.
Today we are joined by MiniRoboFab, who are working on testing the limits of human-robot coworking with a small, sheet-metalworking smart factory.
Their all-star team includes:
- Ritherdon Ltd. & Co – Manufacturing company (UK)
- Nicola Ellis – Artist (UK)
- Digiotouch OU – Technology supplier (Estonia)
So let’s jump into the interview!
Hello, thank you for joining us! Could you define the project in one short sentence?
Ritherdon Ltd. & Co (Manufacturing SME): This project will be Ritherdon’s first step into human-robot working and IoT connectivity within the factory, combined with a study into creating a ‘waste-powder’ paint finish as a new, eco-friendly product option for the company’s customers.
Nicola Ellis (Artist): The project is about trialling Robotic and IoT technology for the purpose of spatial and economic efficiency, waste reduction and the development of new systems and products in a steel enclosure manufacturing process.
(Digiotouch OU) Tech provider: Robotics and the IoT-powered digital transformation of the factory will introduce new capabilities in terms of eco-friendly Lot Size One production and waste reduction.
Why did you decide to apply to BF?
Ritherdon Ltd. & Co (Manufacturing SME): The generous grant, support from the Better Factory team and the opportunity to collaborate with other companies, helped to de-risk and therefore catalyse what is a more ‘blue sky’ product and production development project for the MiniRoboFab partners.
Nicola Ellis (Artist): I had an existing relationship with Ritherdon who are the SME in my KTE. After collaborating with them for 3 years to learn about the existing systems and working culture in the factory I was keen to have input into some kind of new infrastructure. This means I would not only be observing and making artworks which respond to the factory ecosystem – which does have a certain kind of effect on the working culture and how the company is perceived by its community – but I would actually be influencing the company’s future in a practical way and cementing our collaboration through new bespoke products offered to their customers. Before the KTE I had also taken the first steps to produce artworks with technology used in manufacturing, so I was excited by the idea of doing this in a more intense way with robotics and IoT.
Digiotouch OU (Tech provider): Better Factory is providing cutting-edge tools, mentoring, financial support for a mini-consortium to deploy Robotics and IoT technologies paving the way for digital transformation in factories.
How did you come up with the project idea?
Ritherdon Ltd. & Co (Manufacturing SME): Ritherdon had been considering the potential benefits of robot-assisted manufacturing in the factory for some time. As an ISO 14001 accredited company we were also aware of waste powder being a significant issue for the company. So, when the Better Factory opportunity came along, the MiniRoboFab team already had the ideas for the project half-formed.
Nicola Ellis (Artist): The starting point was the challenge put forward by Ritherdon. As a trio we worked together to continuously propose suggestions from our own specialisms in response to this challenge until the individual solutions came together at a point in which they became physically possible. Every suggestion brought us closer to the point of the defined project. However, the defined project is structured to be flexible enough to address the challenge and allow other unexpected knowledge to emerge from the process.
(Digiotouch OU) Tech provider: Digiotouch worked closely with Ritherdon and Nicola at the application stage, understanding and augmenting their idea with Robotics and IoT technologies. These discussions helped us to narrow down the scope of the project as well as figure out how such advanced technologies can be exploited to introduce novel forms of digital transformation at Ritherdon factory.
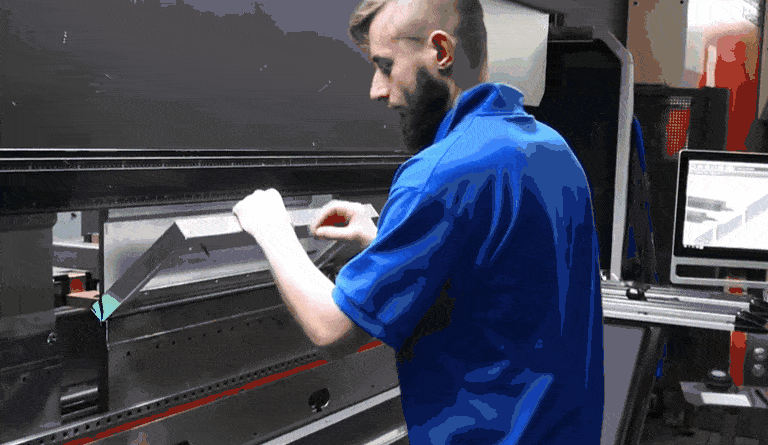
How do you think BF will help you?
Ritherdon Ltd. & Co (Manufacturing SME): This project will be setting up robot-human fabrication within the Ritherdon factory years ahead of when it would normally have happened. Working with the Technical partner, Digiotouch, and using the RAMP platform will also give the Ritherdon factory a boost along the Internet of Things journey. By catalysing these steps, the Better Factory project will accelerate manufacturing efficiency in the factory.
Nicola Ellis’ work with Ritherdon will help reduce the factory’s impact on the environment, by reducing waste, as well as developing a new commercial product for the company.
Nicola Ellis (Artist): I think this project will expand my understanding of new technologies and robotics, specialist language and story communication , which will of course be useful in this project timeline and also as crossover knowledge for future projects, along with potentially generating opportunities to work in other collaborative partnerships in the future.
My relationship with BF and my mentors will help me develop a broader understanding of how artists can collaborate with manufacturers and technology provider to positively influence the future of enterprises, which is beneficial for me, for contextual reasons in relation to my work and for future professional opportunities in my career.
I think I will also gain a better understanding and support with understanding other specialist language and terms, particularly technology, business and presentation to people outside of the art context. This experience will also give me a supported experience in collaborating with a much larger team than I am used to, particularly internationally and through digital means.
This experience will also develop a specific part of my practice at the right time for me, which is the capacity to communicate the story of my collaboration to other people and how to co-create knowledge rather than simply lead or manage project as an individual.
(Digiotouch OU) Tech provider: From a tech provider perspective, the adoption and deployment support regarding the RAMP IoT Platform are essential. In addition to that, the financial grant allows us to grow our operations further in the manufacturing sector.
What are the economical, technical and societal impacts of your project (main impact of each category)?
Ritherdon Ltd. & Co (Manufacturing SME): The main economic impact of the project, for Ritherdon, will be the accelerated improvement of manufacturing efficiency in its factory. The Ritherdon staff will also get the opportunity to develop new skills in IoT and robotics technology. In addition, Ritherdon are hoping that there will be a significant benefit to society from reusing the waste powder in its finishing plant.
Nicola Ellis (Artist): I think the project is a good example of companies collaborating in a way that promotes efficiency and the constant effort to improve manufacturing processes is a positive societal message. The project demonstrates the positive impact of minimising use of resources, minimising waste production, improvement of employee working conditions and increasing the sense of agency people in a factory can have over their working environment.
Ritherdon’s products are positioned in key places in the community, including public places in towns and directly inside peoples homes. Developing a new visual language for these functional ítems which also reduces the amount of waste material that leaves the factory demonstrates that the visual impact these functional ítems have on people’s lives on a daily basis is important, and the products can be more than simply functional containers. The products can contribute to the visual culture of an area in the community and their production can utilise technology in a positive and creative way to make this possible.
I think the project demonstrates how collaboration between different specialisms and ‘joined up thinking’ by different sectors is good for communities and workplaces. It generates creative solutions for challenges that might not have existed otherwise.
Digiotouch OU) Tech provider: For Digiotouch, the technical impacts are firstly deploying an IoT platform in a factory leading to new capabilities, and secondly integrating the tools developed in this project into Digiotouch’s Paradise Platform, enhancing its commercial offerings.
Better Factory is providing cutting-edge tools, mentoring, financial support for a mini-consortium to deploy Robotics and IoT technologies paving the way for digital transformation in factories.
Digiotouch OU (Tech provider)
How do your employees perceive the project? Do they have any previous training or predisposition to use the proposed new technologies?
Ritherdon Ltd. & Co (Manufacturing SME): Ritherdon has a strong continuous improvement culture, so its staff are generally used to and interested in new ideas for improving efficiencies. There has already been significant interest and discussion about how the robot will work in the factory. Most of the staff at Ritherdon have worked with Nicola the artist before and always enjoy the extra creativity that this injects into the regular, day-to-day work.
Is art a motive of change in the world of robotics?
Nicola Ellis (Artist): I think art and robotics both require innovation and thinking beyond what already exists, so in that way I think it is possible for each speciality to recognise each other as motives for change in their respective field. I think the BF project will provide hard evidence that art can be a motive for change in the world of robotics[EC2] , yes. Like any new developments, I think there has to be examples of success and collaboration to motivate further development.
(Digiotouch OU) Tech provider: Yes, there are definitely some synergies present in this Better Factory project in this regard.
What advice would you give to a company that wants to take part in a project like this?
Ritherdon Ltd. & Co (Manufacturing SME): Find partners that you like and can work well with. Also, if you can manage and mitigate the potential pitfalls, then don’t be afraid to try more experimental projects.Artist: It is surprising how much is learned about a specific element of a company, process or practise right from the start of a project like this. In my experience, this is a very positive thing. My advice would be to be open minded and enjoy talking about the possibilities of what could happen, even if the approach is much more different to what would usually take place in the company.
(Digiotouch OU) Tech provider: Digiotouch is your technology providing partner 😉. We have a long history of undertaking and successfully delivering such projects, so I always suggest to other start-ups and SMEs to apply for a project like this.
If you’d like to learn more about MiniRoboFab and their experiment, don’t forget you can check out their KTE page here, including a cool video!