Over the next couple of weeks we’ll be running a series of 1:1 interviews with the KTE (Knowledge Transfer Experiment) teams that joined Better Factory through our first open call. These incredible teams are each made up of a SME, artist and technology provider, working together to develop new and personalized products, become cyber-physical systems, and transforming into Lean-agile production facilities.
OCD 3D is working on the optimization of digital craftmanship in 3D printing. Together they are collaborating to increase the speed and quality of large-scale additive manufacturing processes through AI-enabled process optimization and design specifications.
Their KTE team includes:
- The New Raw – Manufacturing company (Netherlands)
- Gareth Neal – Artist (UK)
- Artific Intelligence (AI) – Technology supplier (Finland)
So let’s jump into the interview!
Hello, thank you for joining us! Firstly, could you tell us why you decided to apply to Better Factory?
Gareth Neal (Artist): We are always looking to push the boundaries of craft and design and embrace the latest technologies and manufacturing processes that allow us to do that. The opportunity to collaborate with both a manufacturer and a technology provider is a really unique and interesting concept, that we believe all parties will hugely benefit from. As an artist we want to create innovation and breathtaking work that the world hasn’t seen before. Only by pushing the boundaries of manufacturing and craftsmanship are we able to that.
Artific Intelligence (Technology supplier): As a technology provider, we are interested and invested in learning and developing new technologies that are used in optimizing manual and digital production processes for both economical and environmental benefits. Factories often have repeatable and unoptimized processes that require manual human labor, which we will try to at least partly optimize and automate using machine learning and artificial intelligence methods. We believe that customized machine learning solutions play a key role in achieving this convergence of different technologies, designs, and goals. Better Factory KTE provides an opportunity to work in an interesting amalgam of manufacturing, artistry, and technology, where we can provide our expertise to improve the ecological footprint of the SME manufacturing process.
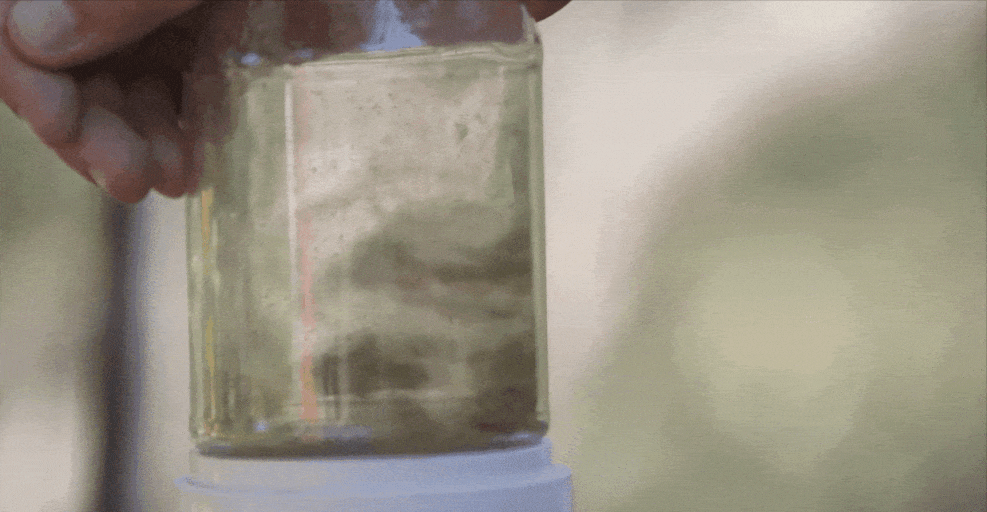
How do you think that Better Factory will help you?
Gareth Neal (Artist): The Better Factory project grant provides us with both the time and the network to be able to develop new work. We wouldn’t otherwise have met with our manufacturers and technology supplier and this unique combination of businesses will hopefully allow for a special and surprising outcome. The project will help is to explore and realise concepts that could otherwise have never left the sketchbook.
Artific Intelligence (Technology supplier): We believe that Better Factory will help us understand the difficulties and challenges of the manufacturing process from the initial blueprint design to the finalized production-ready product. By understanding what each manufacturing stage contains, be it workflow or product-related, we can better collaborate with the SME in building a more agile production facility. We also believe that Better Factory gives us an opportunity to find interesting industry connections and connect us with people that share the same ideals of how the future should be built.
Better Factory provides an opportunity to work in an interesting amalgam of manufacturing, artistry, and technology, where we can provide our expertise to improve the ecological footprint of the SME manufacturing process.
Artific Intelligence (Technology supplier)
Why is recycled plastic furniture made through robotic 3D printing? What are the advantages of this combination compared to the use of conventional plastics or other materials?
Gareth Neal (Artist): This process utilises a material that could otherwise end up as waste. It reuses what we already have to make something new and prints in a controlled and precise way, eliminating yet more waste from the manufacturing process. Plastic is a contentious material in the world of high-end craft and has never been associated with craftsmanship and handwork. As an artist and designer who likes to ask questions with the pieces we create and provoke a reactio,n we embrace this challenge to bring plastic to the world of luxury art and craft.
How does the optimisation of digital craftsmanship in 3D printing benefit health?
Artific Intelligence (Technology supplier): Our main goal in this experiment is to provide optimization of the additive (3D) printing process. We are developing machine learning and monitoring technologies, that lead to a faster and more reliable printing process, which in return leads to better fault detection and smaller waste production. Our secondary goal is to refine and build a more digitalized, documented, and agile production workflow, that can improve and support the SME employee well-being.
What are the economical, technical and societal impacts of your project?
Gareth Neal (Artist): This manufacturing process specifically with the material of recycled plastic hasn’t yet been accepted into the world of craft. By using this material to create beautiful objects we hope that this will add value to the (at present) undervalued material. Plastic is seen as a single-use material, which is totally at odds with its ability to last for hundreds of years. In a societal sense we hope for people to see that this material can have beauty and be desirable beyond only functional products.
Artific Intelligence (Technology supplier): We believe that if the development proceeds as planned, our KTE prototype solution can help to optimize the SME print quality temperature-related problems, and lead to a more reliable production of 3D-printed products with lowered waste-yield. The real-time thermal imaging and machine learning solutions that we are developing allow us to monitor the localized temperature and – in the best case – to predict the accumulation of heat in the printing material. As the melting and hardening of the used material in the additive printing process is highly dependent on the temperature, monitored process control and accurate temperature control of the material layer are needed for achieving high production quality. In addition to the industry-level benefits and impact, we also believe that the thermal imaging machine vision-based solution could scale vertically from industry-level to a more low-cost small-business and customer-level 3D printers and solutions. As these technologies become even more accessible and available, there is a need for the know-how of how the thermal profile of different materials and prints might affect the printing process and quality.
How do you think the demand for recycled plastic furniture has evolved over the last decades and what future do you expect?
Gareth Neal (Artist): Plastic furniture is ubiquitous within many social settings, however it is currently mass-produced and often perceived to be a sterile product. Our aim is to bring tactility and a handmade feel to our plastic furniture by creating patterns and textures with irregularities and subtle colour changes that nod to the handmade. By utilising the printing a robot-like human arm, we hope to embed historical processes like weaving and stitching in the designs.
If you’d like to learn more about this team and their experiment, don’t forget you can check out their KTE page here, including a cool video!