Over the next couple of weeks, we’ll be running a series of 1:1 interviews with the KTE (Knowledge Transfer Experiment) teams that joined Better Factory through our second open call. These incredible teams are each made up of a SME, artist and technology provider, working together to develop new and personalised products, become cyber-physical systems, and transforming into lean-agile production facilities.
The Shoes in Circle project aims to create a custom circular shoe model, by automating the (re)manufacturing process in combination with parametric design, adding the optionality for personalisation.
Their KTE team includes:
- Tapi-1 Aleksander Żur (Manufacturing company)
- Anka Walicka Projekt (Artist)
- Studio GF&L Unipessoal, Lda (Technology Provider)
Let’s get started with the interview!!
Hello, thank you for joining us! To start off, could you tell us why you decided to apply to Better Factory?
SME Tapi-1 Aleksander Żur: Tapi is a family company with a long tradition of making shoes. My grandfather started making shoes in 1950. In our history every 10-15 years there was a new technology or machine that made a big impact to how we make shoes. With all new technologies from Circular Knitting, through IoT, up to Robotics, we see a possibility to fundamentally change how shoes are made. But we need a help with all this new technologies and fresh way of looking at things. With Better Factory we have all the support we could dream of. That is why my company applied.
Artist Anka Walicka Projekt: As an artist, I chose to apply to Better Factory for several reasons. Firstly, I love challenges and the opportunity to experiment with new ideas. This will give me a chance to develop my creativity and create unique solutions in the field of footwear.
Secondly, I aspire to be part of a team that focuses on innovation and collaborates with various industries. I have the chance to contribute to the advancement of the footwear industry by experimenting with new technologies and materials. I would like to be part of the change and create footwear that is not only aesthetic but also functional and sustainable.
Tech provider Studio GF&L Unipessoal, Lda: My background is in the shoe manufacturing business – I have worked for many years in this field. In 2019, I was looking for ways to automate shoe manufacturing at my own factory. I didn’t find any solutions that were satisfying, so I assembled a team and started looking into robotics to make my own solutions. My team created solutions for shoes manufacturing industries based on cobots that are easy to use. With Better Factory we will have an opportunity to show our solutions to new markets, as well as access the know-how needed to grow our business and help other companies in the shoe manufacturing business.
“With all new technologies from Circular Knitting, through IoT, up to Robotics, we see a possibility to fundamentally change how shoes are made. But we need a help with all this new technologies and fresh way of looking at things. With Better Factory we have all the support we could dream of.”
SME Tapi-1 Aleksander Żur
Can you explain the circularity concept of Shoes in Circle and how it differs from traditional shoe production methods?
SME Tapi-1 Aleksander Żur: The process of making traditional shoes takes multiple steps. To keep it simple first you need to design the shoe, then cut it out of materials like leather or fabric. In the next step you need to stitch it together to get an upper. When upper is ready you can make a final assembly – attach sole to upper – and now you get your typical leather or textile shoes.
There are leftovers from cutting leather and textiles. During a production some elements needs replacements (for example due to leather defects visible only at final assembly stage). In your typical shoes you will find leather, cardboard, fiberglass, multiple types of textiles, nails, several types of cement. In other words there is a lot of waste, and final product can’t be easily separated into different materials. So the recycling is hard.
Uppers made with circular knitting technology offers great simplification of production process. Machine knits the upper using recycled yarns – it is additive process with almost no waste created. Then you attach upper to sole and the shoes are ready. But this time they do not contain cardboard, fiberglass, nails, and many other materials. So it is easy to separate materials and recycle it compered to traditional shoes.
Artist Anka Walicka Projekt: Circularity in the context of Shoes in Circle for footwear created from sole components and knitted uppers with innovative construction techniques refers to the application of sustainable design and production practices that minimise the negative impact on the environment by using a single type of material without the need for separating individual components during the shoe recycling process.
The difference between the circularity of footwear production and traditional methods lies in the approach to sustainability and waste minimisation. In traditional footwear production methods, multiple different materials are often used, which are bonded together using adhesives and stitching. This complicates the recycling process and often leads to a significant amount of material waste generation.
On the other hand, the concept of circularity in Shoes in Circle aims to design the product in a way that its overall material composition is as simple and homogeneous as possible, facilitating recycling and reuse. The use of knits and seamless techniques reduces the amount of production waste, while the application of sustainable materials minimises the negative impact on the environment.
What role does the artist play in this project, and how do they collaborate with the tech provider and manufacturer?
Artist Anka Walicka Projekt: I believe that my role as an artist-dreamer in this experiment plays a crucial function in integrating creativity, ecology, and an innovative approach to footwear design and production.
The artistic process is a journey of exploring new paths, changing directions, overcoming failures, and constantly starting anew.
The main goal of my involvement in this project is to develop skills in circular knitting for footwear and implement parametric design into the footwear production process. Together with the technology provider and manufacturer, we form a diverse yet fully integrated and dynamic team that harmoniously blends the organisational and creative aspects of the project with technical feasibility.
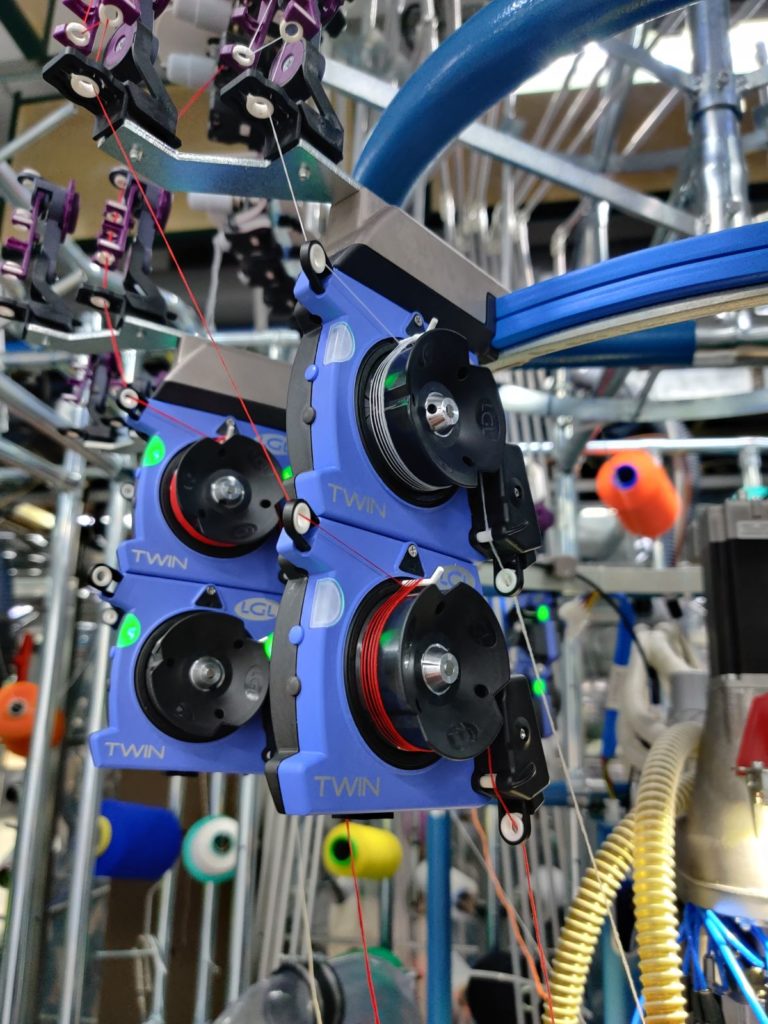
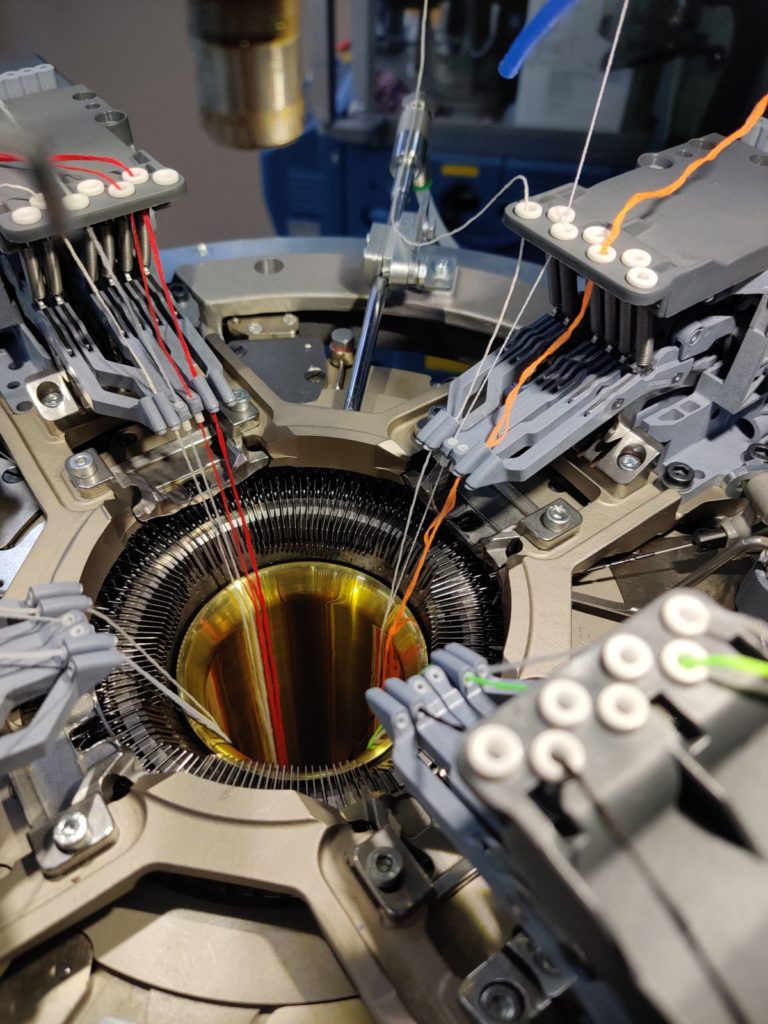
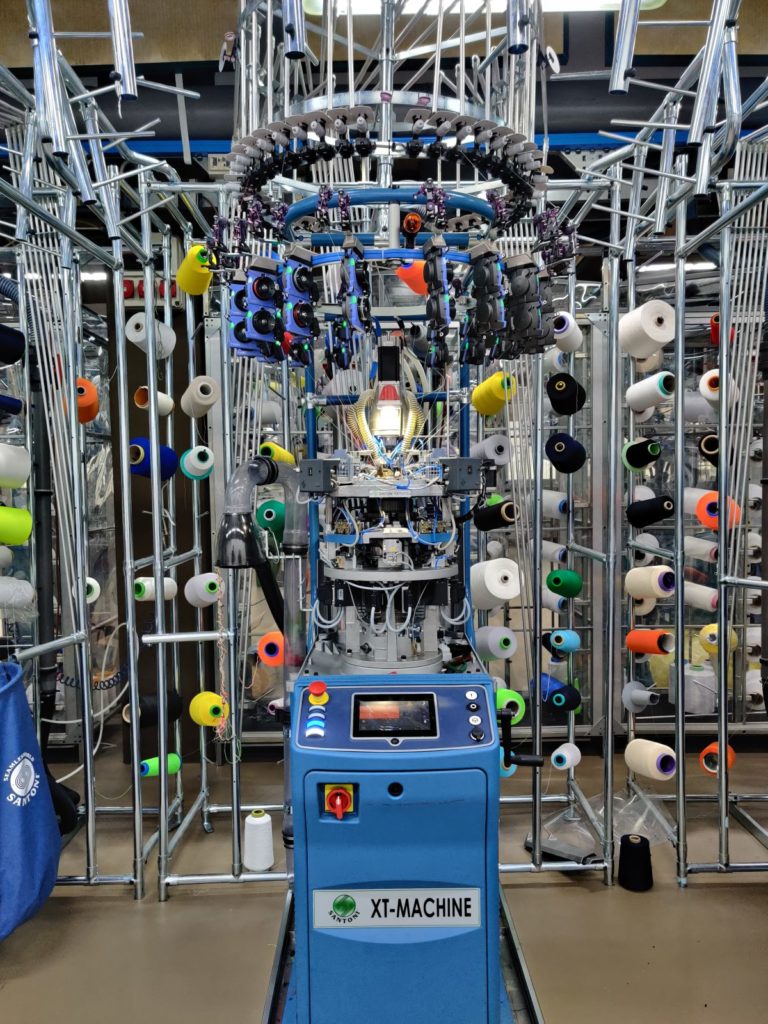
Can you explain how the robotic processing line will improve the (re)manufacturing process and how it relates to circularity?
Tech provider Studio GF&L Unipessoal, Lda: The idea is to use cobot to help with manufacturing of traditional shoes as well as circular knitted. One of the steps in manufacturing all type of shoes is attaching sole to upper. Usually it involves applying cement onto upper. It is a precise job that needs a steady hand. If the cement is below the required line then the sole will not stick to upper. If the cement is over the line it will create a second grade quality shoes that needs to be reworked or sometimes disposed off.
With robotic arm applying cement we will be able to reduce amount of cement, as well as reduce quality issues to zero – this way helping reduce the waste created.
Can you describe the impact of minimising workers’ exposure to leather dust and how it will be achieved?
Tech provider Studio GF&L Unipessoal, Lda: In traditional manufacturing you need to perform roughing of leather. If you don’t then the sole sill not stick to the leather. It is a process where you scratch surface of the leather using for example sandpaper or metal brush. The sand paper is revolving at high speed and the operator is pushing the leather against it. This operation requires great physical strength from a operator, as well as a lot of precision. If you push the upper too hard, sand paper will make a hole in it – thus you need to replace an element and create a lot of extra waste. As you can imagine, a fast spinning metal brush with contact on leather creates a lots of small particles – a leather dust.
With the cobot the operator, we just place the shoe in a special stand and the robot arm does its job. The robot will not apply too much force, so you will not have to deal with holes in elements that need to be replaced. Secondly, the operator does not need to keep close eye on the process – so physically there will be a greater distance from dust to operator. Thirdly, the roughing tool is designed in a way that reduces the amount of dust in the first place and secondly with a special suction device collects most of the dust that is created.
In summary, the booth operator exposure to dust as well as waste from errors will be reduced.
“With Better Factory we will have an opportunity to show our solutions to new markets, as well as access the know-how needed to grow our business and help other companies in the shoe manufacturing business.”
Tech provider Studio GF&L Unipessoal, Lda
How do you foresee that this experiment might inform future collaborations between artists and manufacturers?
Artist Anka Walicka Projekt: I think that an unconventional approach to shoe design can encourage both artists and manufacturers to have a greater need for collaboration and the exchange of ideas, which can lead to the development of team projects that combine artistic creativity with the technical knowledge of producers.
Such experiments may prompt manufacturers to understand that their role can extend beyond traditional production tasks, and collaboration with artists can potentially support original artistic projects and inspire the implementation of new technologies and engineering in the production process.
I hope that projects like ours will influence manufacturers, stimulating them to recognise the market potential for unique and innovative products.
If you’d like to learn more about SHOES IN CIRCLE and their experiment, don’t forget you can check out their KTE page here!