Over the next couple of weeks we’ll be running a series of 1:1 interviews with the KTE (Knowledge Transfer Experiment) teams that joined Better Factory through our second open call. These incredible teams are each made up of a SME, artist and technology provider, working together to develop new and personalized products, become cyber-physical systems, and transforming into Lean-agile production facilities.
The SMARTVIEW project aims to develop and demonstrate a nature-inspired holistic interface for cross-factory cooperation.
Their KTE team includes:
- SME Famolde (Manufacturing company)
- Kristina Pulejkova (Artist)
- Octavic (Technology Provider)
So let’s jump into the interview!
Hello, thank you for joining us! To start off, could you tell us why you decided to apply to Better Factory?
SME Famolde: Better Factory presents a different project approach by putting an artistic touch into complex production processes which are the industrial scenarios.
As per our strategy of looking at people as key elements of business success, FAMOLDE found in Better Factory the opportunity to reach out to people, through unconventional tools, but in a way that will facilitate the commitment of workers in the productive ecosystem. As partnership facilitators, Better Factory put key partners on the same route to achieve this purpose and, therefore, from the first interaction we believe in the success and benefits of being able to participate in this project.
Artist Kristina Pulejkova: My approach to art making is multidisciplinary and I often work with experts from other fields such as computer science, biology and dance. As I was looking at ways to expand my artistic practice into applied, as well as speculative design, I came across the Better Factory project which was a perfect match.
Tech provider Octavic: Better Factory’s commitment to innovation and advancement aligns perfectly with our passion for pushing boundaries and exploring new frontiers in industrial automation. We are excited about the prospect of working alongside a team that shares our vision and dedication to transforming the manufacturing industry. Joining Better Factory would not only allow us to contribute with our skills and expertise, but also provide an environment where we can continuously learn and grow while making a meaningful impact.
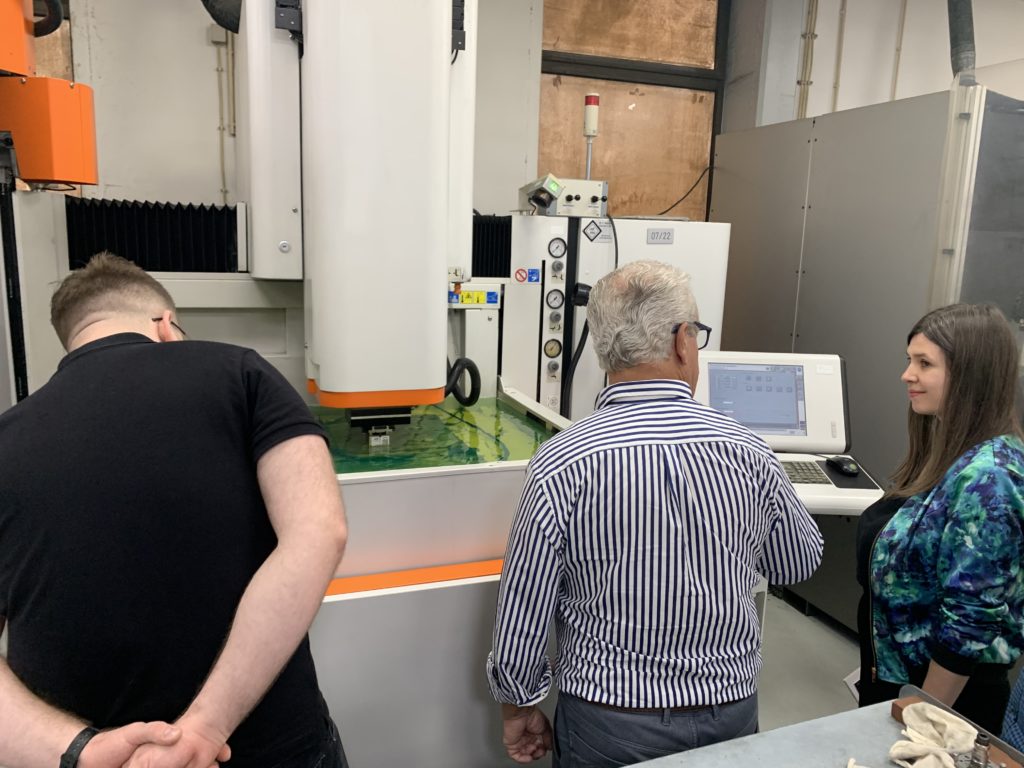
Can you describe the nature-inspired holistic interface that the SMARTVIEW project will develop?
SME Famolde: From the point of view of FAMOLDE, we see artist Kristina’s proposal as something different and inducing change: the fact that the teams are strongly focused on methods and conventional experience, there is no longer room to look at the processes from another perspective, making it impossible to consider any other idea outside the normal flow of the performance. Thus, the approach through parallelisms of nature, allows to model the reasoning in a more natural and sustained way, sometimes uncomplicating what in a process is only atrophied by factors that we add as a precaution, but that are not necessarily a benefit for the agility of the processes or problem solving.
Artist Kristina Pulejkova: For SMARTVIEW, the idea is to take inspiration from mechanisms and strategies found in nature. Natural systems and collectives present excellent case studies for productivity and energy efficiency strategies. Leaf-cutter ants are optimising leaf size and weight for efficient transport, bees build hexagonal hives for best use of space, and slime mould – a single celled organism can be used to calculate fastest routes from A to B. Forests are in fact interconnected systems, receiving data on potential predators, threats, and weather conditions kilometres away, thanks to the underground mycelial network built by mushroom – tree symbiosis.
Through taking inspiration from different biological and behavioural models deriving from nature, like the above-cited examples as well as real-time data from the shop floor, the aim of the artistic process will be to present a visual platform that flattens the management hierarchy system, and imagine the factory as an ecology. In doing so, the idea is to inspire a different point of view of the factory’s processes, enabling workers to feel more connected to each other and to see the factory as a whole towards an improved wellbeing.
Tech provider Octavic: Engagement from the shopfloor employees is critical to a successful company. Having them interacting with higher management in improving their work and output will ultimately lead to results that might’ve not been possible through traditional management methodologies/approaches.
“Natural systems and collectives present excellent case studies for productivity and energy efficiency strategies. Leaf-cutter ants are optimising leaf size and weight for efficient transport, bees build hexagonal hives for best use of space…”
Artist Kristina Pulejkova
How will the artist Kristina Pulejkova use VR and data analytics to build narratives around human-nature relationships in the context of the factory floor?
Artist Kristina Pulejkova: Immersive technology such as AR,VR, physical computing and data analytics will be used to create a performance overview platform with an organic interface inspired by nature-based strategies, reimagining the dashboard for the industry 5.0. Through use of mixed reality, haptics, interaction design and real-time data, the idea is to use ecologies and natural processes as metaphors and design inspiration for creating a more organic overview of the factory process. Often called the empathy machines, technologies like VR have the ability to transport people into different worlds as well as give them a unique point of view. The plan is to utilise this power of VR to imagine the factory of the future.
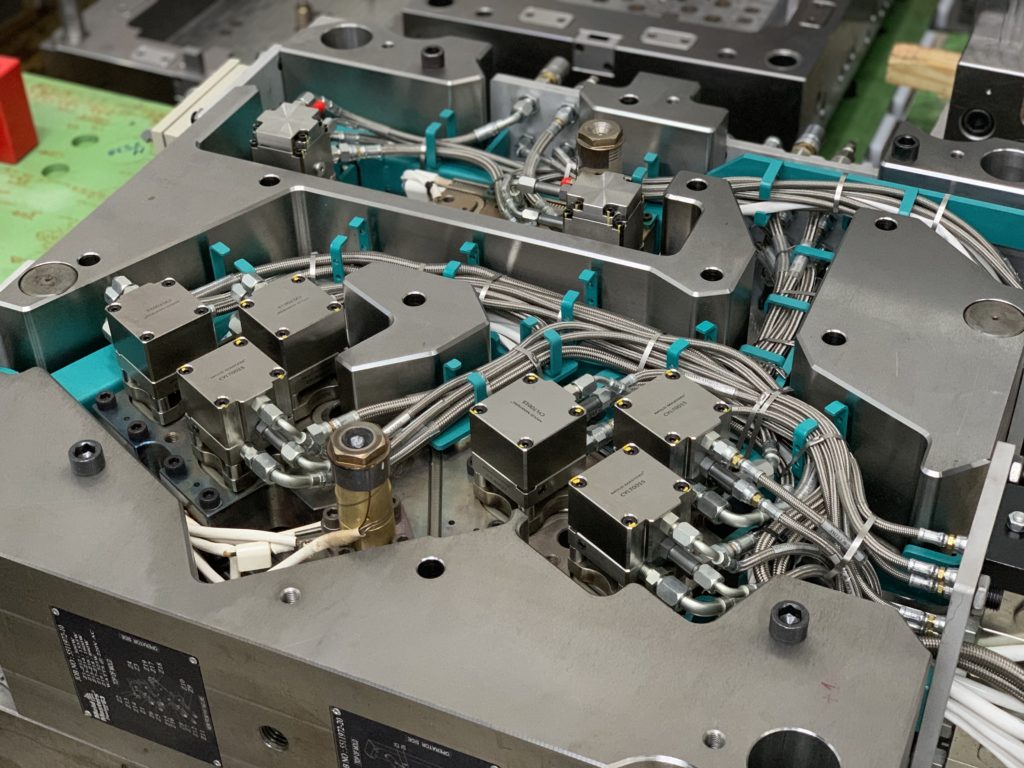
How do you envision the factory as an ecosystem, and how will this approach help address the silo mentality across Famolde’s departments?
SME Famolde: FAMOLDE is an industrial company with almost 40 years of existence that has gone through several structural changes, but which has always maintained a family spirit. However, the constant market fluctuations and adversities that we have been experiencing in recent decades, have been transforming teams from different sectors, distancing them more and more. The SMARTVIEW project intends to break this distance in professional inter-team relationships, through a tool that facilitates the perception of performance impacts between departments, and awareness of the commitment to shared success, not only of the teams, as well as of the company as a whole and of the industrial group where it operates. Deep down, what is expected is a reformulation of internal relations, and that these become more agile and intrinsic in the context of the shop floor.
Artist Kristina Pulejkova: The idea of a factory as an ecosystem will be exploring the potential to bring people together and inspire them to function as a more integrated unit, shifting the production dynamic from the individual to the factory as an ecology or a whole. Using narrative design and gamification strategies to reshape factory narrative, can lead to finding new innovative ways for employees to find mutual ground across departments, and create better relationships through gamified experiences, where employees are moving towards a common goal.
By developing a visual platform based on non-human communication, the artistic tool will aim to provide a neutral language which will improve the communication across management and shop floor workers. Employees will be invited to venture outside of the human scale and engage with the factory’s day to day processes as an ecosystem and observe their roles through a unique perspective and scale. The process of stepping out of the already established roles within the factory, would allow for new connections to be made between management and shop floor employees, building interdepartmental connections based on shared goals.
Tech provider Octavic: We envision the factory as an ecosystem where every department and process is interconnected, working in harmony towards a common goal. This approach fosters collaboration, communication, and knowledge sharing among different departments within Famolde. By breaking down the barriers of silo mentality, we can eliminate the isolated thinking that often hinders productivity and innovation.
In this ecosystem, each department becomes an integral part of the larger whole, contributing their unique expertise and insights. By promoting cross-functional collaboration, we can leverage the diverse skill sets and perspectives within Famolde to drive efficiency, streamline processes, and optimise performance.
“We envision the factory as an ecosystem where every department and process is interconnected, working in harmony towards a common goal.”
Tech provider Octavic
What specific impacts do you hope to achieve through the SMARTVIEW project?
SME Famolde: The greatest impact will certainly be the improvement of current production processes, in terms of agility, as well as production results and performance indicators. On the other hand, and from a technical and functional point of view, an improvement in communication efficiency and a reduction of GAP’s in decision-making is as well expected: human experience, combined with productive data, will form a sophisticated alliance in the articulation of processes and, above it all, reduction of costs and productive times. These impacts not only benefit the company’s competitive capacity but will also translate into greater personal fulfillment for workers and a better quality of life, where they will not have to spend extra hours to complete jobs resulting from inter-departmental inefficiencies.
Tech provider Octavic: Through the SMARTVIEW project, we aim to achieve several specific impacts that can greatly benefit the organization. Firstly, we envision enhancing operational efficiency by implementing real-time data visualization and analysis capabilities. SMARTVIEW will provide us with a comprehensive view of our manufacturing processes, allowing us to identify bottlenecks, optimise workflows, and make data-driven decisions to improve overall productivity.
Secondly, we hope to improve quality control through SMARTVIEW. By integrating visual management boards and leveraging machine interaction, the team can closely monitor the quality of their products throughout the production cycle. This will enable the team to detect issues early on, implement corrective measures promptly, and maintain high standards of product quality, ultimately enhancing customer satisfaction.
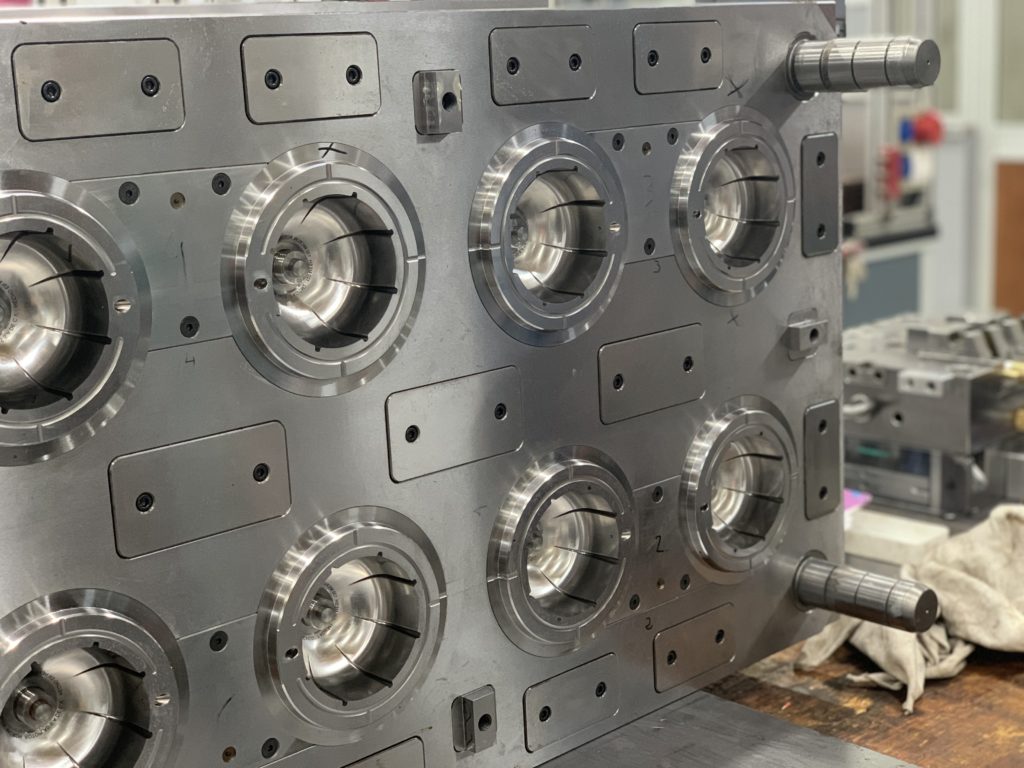
Are there any specific numbers or percentages you are aiming for in terms of reducing lead-time, waste, increasing machine availability, saving energy consumption, and reducing GHG?
Tech provider Octavic: We will aim to increase machine availability through the downtime monitoring feature that our system has. Tracking down any potential issues that could develop into more serious problems/breakdowns will help reduce the lead time as well, since the machine is running more efficiently and with less and less stoppages.
In terms of waste, tracking the defects that are being recorded by the operators, their root cause can be isolated and avoided/removed in the future.
What do you foresee for the future of the project, after its end, in terms of future applications or learnings within the industry?
SME Famolde: The project will certainly bring something different to the context of the organization and that will contribute to the well-being of the workers. The management teams will have the opportunity, during the project, to make a diagnosis and identify some failures, in order to model their processes, as a way of continuous improvement. Companies are made of people: the more people feel fulfilled, the more sustainable the company becomes. Above all, the lessons to be learned from the project will help adapt the vision to better plan future strategies where, due to the latest experiences felt at the world level, they may vary adversely and drastically.
If you’d like to learn more about SMARTVIEW and their experiment, don’t forget you can check out their KTE page here!