Over the next couple of weeks, we’ll be running a series of 1:1 interviews with the KTE (Knowledge Transfer Experiment) teams that joined Better Factory through our second open call. These incredible teams are each made up of a SME, artist and technology provider, working together to develop new and personalised products, become cyber-physical systems, and transforming into lean-agile production facilities.
The STARIOT project will focus on professionalising the production of wheat stems, as well as creating more opportunities for products made from said wheat stems. The Staramaki factory will be upgraded with industry 4.0 technology, allowing for data analysis in the harvesting, transport and production processes.
Their KTE team includes:
- Staramaki (Manufacturing company)
- Gilbert Sinnott (Artist)
- CommonsLab (Technology Provider)
Let’s get started with the interview!!
Hello, thank you for joining us! To start off, could you tell us why you decided to apply to Better Factory?
SME Staramaki: Better Factory offers a collaborative environment where SMEs can work with new teams and meet other professionals, including experts, mentors, and potential partners. This networking opportunity can lead to valuable collaborations and synergies.
Better Factory is known for supporting innovation and the adoption of new technologies. Through our participation in Better Factory, Staramaki can access resources, tools, and expertise to improve and optimise its production processes. Staramaki can explore and test cutting-edge technologies that may enhance its products, services, or operations. This could lead to increased efficiency, reduced costs and improved overall performance.
Better Factory focuses on sustainability and circular economy practices. For Staramaki, this presents an opportunity to explore new ways to repurpose waste materials generated during the production process, potentially creating additional revenue streams and reducing environmental impact. This could lead to the development of innovative products and the expansion of its product portfolio, catering to a broader market and customer base.
Artist Gilbert Sinnott: I was originally forwarded the application by artist Martin Nadal, creator of FANGØ, with whom I’d had fun modifying a Macintosh 128K at our studios in Berlin. The Better Factory project has a confluence of ideas around art, technology and industry that really struck a chord, and made writing an application flow freely, in particular as a direction I’ve been headed. My work is very much practice-based, so I balance periods to experiment, iterate and develop prototypes, and periods to apply those prototypes, for example in my video or performance works as Autr. In the long-term I’m interested in how art can converge around practical and environmental problems, and how this can harmonise in creative and technological fields. There’s lots to explore and discover, and I think this is best done when people from all walks of life cross-pollinate and collaborate, so I am very enthused by the project.
Tech provider CommonsLab: CommonsLab had previously worked on automation and remote sensing applications in small industries on Crete, especially with wineries. So when we saw the open call published by the Better Factory project, it seemed to us like a perfect opportunity to help some of the less digitised businesses of Greece towards a more efficient and automated production. Especially, the Staramaki cooperative was a love at first sight, since their philosophy of sustainable and ethical production resonates with many of the ideas, which CommonsLab also holds dear. The match with Gilbert Sinnott from Liberated Interfaces, who also focuses on sustainability and upcycling in art and electronics, made an extremely inspiring team.
In the long-term I’m interested in how art can converge around practical and environmental problems, and how this can harmonise in creative and technological fields. There’s lots to explore and discover, and I think this is best done when people from all walks of life cross-pollinate and collaborate, so I am very enthused by the project.
Artist Gilbert Sinnott
What inspired the STARIOT project, and how did the idea come about?
SME Staramaki: The idea for the project emerged from the challenges Staramaki faced in optimising its production processes, as well as swiftly adapting its processes to accommodate new and customised products. Staramaki’s core product, the drinking straw made from wheat stems, embodies the principles of sustainability, circular economy, and social responsibility. However, to further enhance their production processes and adapt to challenges and overcome the typical manufacturing difficulties associated with bio- and nature-based solutions, Staramaki recognised the need for an agile and automated facility.
Some of these challenges included reducing waste, shortening reconfiguration times, implementing customisation of products, and creating added-value products from by-products. To achieve these goals, the concept of STARIOT emerged as a collaborative effort to leverage cutting-edge technologies, such as the Internet of Things (IoT), data analytics, and automation, with focus on reducing waste and utilising by-products, strengthening Staramaki’s circular and sustainable approach to manufacturing.
Artist Gilbert Sinnott: I wrote some code to experiment with 3D polyhedral shapes, and was introduced to the STEMS project by Eleni Karagiannidou at Staramaki, which uses waste straws to construct educational Platonic and Archimedean solids. This was very serendipitous; so for the STARIOT project I will put my skills to work supporting STEMS, and exploring the field further with Staramaki, for example by creating customisable shapes, or tensegrity structures of the kind created by Kārlis Johansons and Kenneth Snelson. I am very interested in bio-organic pattern formation, which is explored in my video works through dynamical systems of feedback, using analogue and digital methods: a mix of organic and inorganic. The geometrical basis of polyhedra is another direction from which to look at pattern formation in nature, and I think there are interesting parallels to this when thinking about the history of computer art, and new technologies like XR and AI.
Tech provider CommonsLab: With a background in developing customised automation solutions for research and industry, as well as with network and IoT deployments, CommonsLab saw the opportunity to use their skills in designing embedded systems to streamline and accelerate the Staramaki production process. This makes it also more agile to adjust for new and customised Staramki products and more transparent, for the purpose of easier HACCP auditing, of better quality assurance, of more precise bottleneck and opportunity detection, as well as for increased consumer awareness, regarding the ecological and social sustainability and circularity. The easiest and fastest solution with best RoI seemed to be a deployment of an RFID material-flow monitoring system with optimised, smart hand-held devices and a central data analytics platform, the RAMP dashboard.
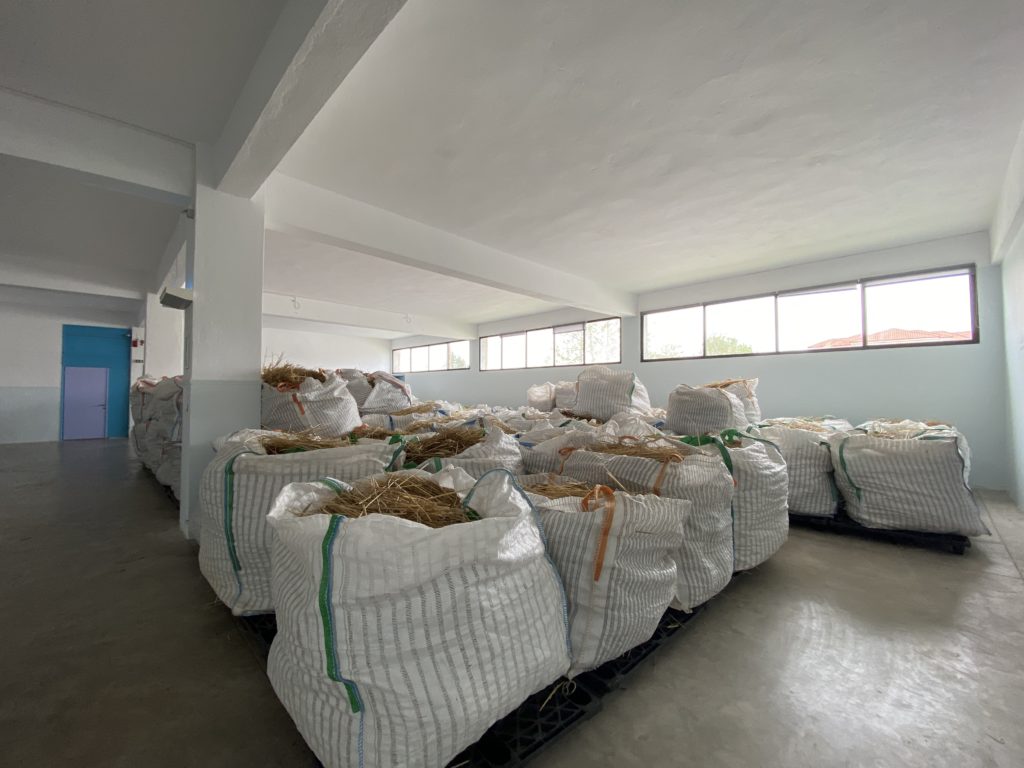
Can you tell us more about the technology upgrades that will be implemented in the Staramaki factory, and how these upgrades will impact the production process?
SME Staramaki: As a manufacturing company we need to monitor and optimise the production parameters to keep track (in the most up-to-date and real-time way possible) of the amount of raw material available, and of the material inside each production step and in buffers in-between production steps. By keeping track of raw material availability and monitoring material movement through each production step and buffers in real-time, Staramaki gains valuable insights into its production processes. This real-time data allows for better decision-making, proactive problem-solving, and resource optimisation.
These upgrades that will be integrated by the Better Factory STARIOT project will contribute to increased throughput, increased safety and decreased human error due to manual processes, so that in the long run production cost will be decreased, time efficiency will be increased and worker well-being will be improved.
Tech provider CommonsLab: The STARIOT project focuses on two main aspects: Firstly, the automatic acquisition of production data, including the details regarding the preparation of the soil, the cultivation of the wheat, the harvest, the material storage, processing and drinking straw production, and eventually the packaging. This data gives not only valuable insights about where and how any of the above steps can be improved or streamlined, but can also be used to convey to the customers the environmental and social value that the product has. Secondly, a set of cameras monitors workers on the production line, to investigate possible improvements to the ergonomics of the workplace. Furthermore, we will assess the possibility of using AI to predict adaptive smart energy usage, depending on demand and on availability of sunshine for the solar collectors, and additionally other automation systems and solutions will be explored throughout the project.
How will data analysis be used in the harvesting, transport, and production processes of the wheat stems, and what benefits do you expect to see from this?
SME Staramaki: Data analysis empowers Staramaki to make data-driven decisions, improve operational efficiency, reduce costs, enhance product quality, and align its processes with sustainability goals.
By analysing historical data and real-time information, Staramaki can make informed decisions, minimising the risk of yield losses. By monitoring energy consumption, raw material usage, and equipment efficiency, Staramaki can also identify opportunities to optimise resource utilisation, reduce operational costs and plan its production schedules more effectively, avoiding overproduction or stockouts. By analysing data on waste generation and material usage, Staramaki can additionally implement circular economy practices, turning waste materials into valuable resources for other processes.
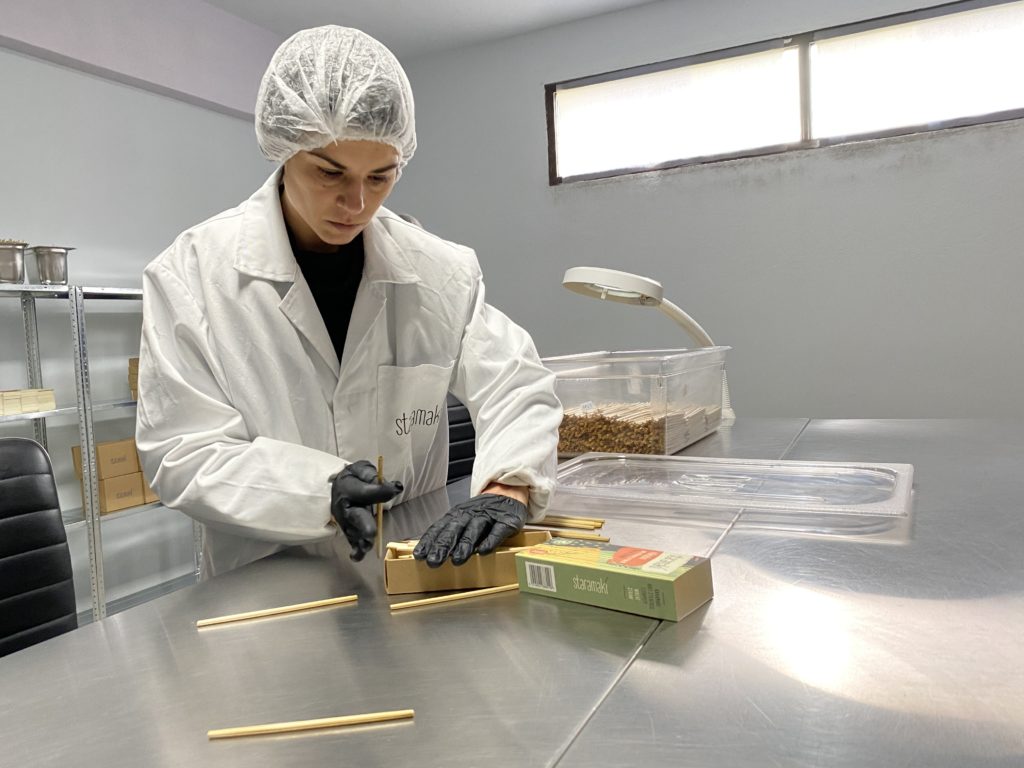
What role does CommonsLab play in the STARIOT project, and how have they supported the project so far?
Tech provider CommonsLab: Up to this point, CommonsLab and Staramaki have examined and analysed which production data has merit to be collected, and devised the optimal way to acquire it with minimal delay to the production, maximal reliability, and optimal ease of use. Based on the insights taken from this collaborative introspection, we have already prototyped a device, which uses NFC communication with RFID tags, firstly to be aware of the material flow and secondly to store data both on the containers for immediate off-line reference, as well as on the cloud for real-time analysis and visualisation. So far, ten of these pilot devices were produced, hundreds of RFID tags were deployed and everything is currently used in the production line of the Staramaki factory.
The insights and lessons learned from this project can be disseminated across the manufacturing industry, fostering a culture of collaboration and collective efforts to address social challenges, inspiring and influencing other manufacturing industries to adopt more conscious and socially responsible practices, contributing to a more resilient future for the manufacturing sector as a whole.
SME Staramaki
How does the artist Gilbert Sinnott fit into the STARIOT project, and what contributions do you expect from his algorithm development work?
Artist Gilbert Sinnott: An immediate challenge is to make the construction steps of polyhedra in the STEMS project easier and easily understood, so I will be looking into creating generative instructions and printable diagrams, and using graph optimisation algorithms to do it. A secondary challenge is to expand these techniques and methods into conjoined and sculptural polyhedra, for example by using natural reeds which are an abundant material in Greece. This will involve fabrication and materials work which will be supported by CommonsLab’s expertise in Crete. While creating the interactive tools, the focus will be on communicating concepts in an accessible way, and I will also be making sure to use nascent WebXR standards, since this is one area where interaction design is quickly moving.
Tech provider CommonsLab: One of the waste streams from the Staramki production line are drinking straws, which have been disqualified due to aesthetic or physical flaws, such as discoloration or cracks. These B-grade stems are envisioned to become building blocks for a new Staramaki product, with which complex polygonal and polyhedral structures can be produced for educational, decorative or practical purposes. Gilbert Sinnott brings in his creative energy to explore how such geometric shapes can practically be built, how they can be generated algorithmically or through a graphical user interface, and how the user can be optimally instructed to build such constructs step by step.
The solutions developed during this KTE can be adopted to other manufacturing SMEs. Especially the many small oil mills and wineries on Crete are an excellent use case for the automated production-data collection, analysis and visualisation, since these small factories often have a great potential to be improved once the bottlenecks and price drivers can be identified better.
Tech provider CommonsLab
Finally, what do you hope will be the lasting impact of the STARIOT project, and how do you see this project influencing other manufacturing industries in the future?
SME Staramaki: STARIOT’s focus on conveying the added value of Staramaki’s ethical production practices can contribute to raising awareness about the importance of supporting socially responsible companies. The integration of IoT, data analytics, and automation in the STARIOT project will showcase the potential of advanced technologies to enhance efficiency, reduce costs, and improve overall operations.
The insights and lessons learned from this project can be disseminated across the manufacturing industry, fostering a culture of collaboration and collective efforts to address social challenges, inspiring and influencing other manufacturing industries to adopt more conscious and socially responsible practices, contributing to a more resilient future for the manufacturing sector as a whole.
Artist Gilbert Sinnott: I started a company Liberated Interfaces this year, primarily as a place to put design and engineering work that sits independently to my artworks. However it also has some loftier goals, which is an ethos for harmonising analogue and digital, and creating resilience for the future. During the course of the project, I hope to solidify some of the ideas I have about design.
For manufacturing industries on the whole, I hope our project will be an example of how it’s not only beneficial to have artists work on practical problems, but also beneficial to broadly apply speculative and collaborative processes to foster innovation.
Tech provider CommonsLab: On the one hand, the impact that STARIOT will have on the Staramaki production facility, sums up to more efficient and more sustainable production. And this in turn means that the European consumers will have access to a top-notch high-quality fully home-compostable drinking straw with a competitive price tag, together with other newly developed products made from the same raw materials.
On the other hand, the solutions developed during this KTE can be adopted to other manufacturing SMEs. Especially the many small oil mills and wineries on Crete are an excellent use case for the automated production-data collection, analysis and visualisation, since these small factories often have a great potential to be improved once the bottlenecks and price drivers can be identified better.
If you’d like to learn more about STARIOT and their experiment, don’t forget you can check out their KTE page here!