Over the next couple of weeks we’ll be running a series of 1:1 interviews with the KTE (Knowledge Transfer Experiment) teams that joined Better Factory through our first open call. These incredible teams are each made up of a SME, artist and technology provider, working together to develop new and personalized products, become cyber-physical systems, and transforming into Lean-agile production facilities.
WRC is working on welded metal door fabrication, design, innovation and automatization of production. Their KTE focuses on shifting a manual production process towards human-robotic welding fabrication for specialized container production.
Their KTE team includes:
- ZOVOS-EKO s.r.o. – Manufacturing company (Slovakia)
- Studio Libertiny s.r.o – Artist (Netherlands)
- Rossum integration – Technology supplier (Slovakia)
So let’s jump into the interview!
Hello, thank you for joining us! Firstly, if you could define the project in one short sentence, what would it be?
Studio Libertiny s.r.o (Artist): We could describe it as the redesign and optimization of our existing portfolio, suitable for automated production.
Rossum Integration (Technology supplier): In one sentence: we are taking on an important task within our company, or rather production plant, which is make production more agile.
Studio Libertiny s.r.o (Artist, Catarina): Just bringing some creative solutions to this environment.
Why did you decide to apply to Better Factory?
Studio Libertiny s.r.o (Artist): Well, a lot of my work is based on experimentation and innovation. I had experience with designing metal furniture with a metal company, where we set up production from scratch for the final product. So it was an ideal combination of artistic talent, or rather creativity, and also an opportunity to innovate in a very concrete way in a real project through a European Union collaboration, across different countries. So, there was something interesting for us there as a studio.
Rossum Integration (Technology supplier): Fortunately, I’m not the first one that started it. I’m just a technical guy and project manager. But from our point of view, why we grabbed this opportunity: we are a young company, so we liked the challenge and we never did something like this from the technical perspective, this digital twin integration. So that’s why we took it as a challenge for us.
ZOVOS-EKO s.r.o. (Manufacturing company): This project is interesting for our company, because we produce special containers. The cost for research into new technology is not so simple for us, so we can use this as a chance to invest into this kind of technology. When part of our cost, the financing will be from this project. So this is our answer.
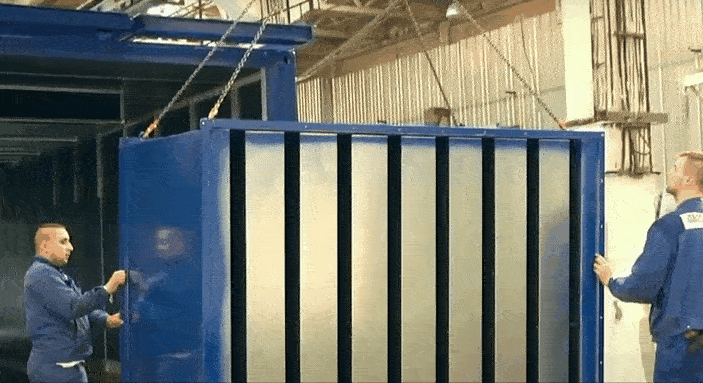
How do you think that Better Factory will help you not only in the project, but also after the project?
Studio Libertiny s.r.o (Artist): Well, the important thing, is that this is a pilot project, so we have no reference of what it can do for other artists or people involved in it. So it’s also pioneering in some sense. We put our trust in the project as well; it goes both ways. For us, so I’m going to speak on behalf of Studio, it is a very good first larger collaborative project that’s also not only involving design and technology, but it’s incredibly complex, which is an interesting part of this project. It’s not only just me and the other participants working together, but the whole process behind it. It’s really interesting to see how large projects like this funded by the European Union work. So in a way, it’s also a learning curve in terms of working on bigger projects that are subsidized and not only within the private sector. But of course, I’m really looking forward to dissemination of the project on a public scale, i.e. when we have it finished and if it’s a success. I learnt that even what doesn’t work is also a success. So that’s part of the experiment; I’m looking forward to sharing it and see the reactions. So I’m looking forward to seeing the impact the project has; whatever you do, you want to have an impact. There’s a certain integrity in the way you work, that the impact is automatically there.
Rossum Integration (Technology supplier): From our side, we said at the beginning of this project that this will be the first welding robot in our production plant. We chose the door now as the first step, I can say, among all the other parts of our major product that make up this special container. We think that we can continue with development of the other parts of our container after the end of this project. We can check the validity of various aspects like the rate of productivity in the production and for other systems or processes, logistics and so on.
ZOVOS-EKO s.r.o. (Manufacturing company): Basically it’s a combination of what the rest of the team has said. This platform with Better factory allows us to try something new with the SME without any huge costs. We can test it and when it’s proven, then we can make it and build it and make something happen, something new. The innovation is here. The future is robotization or automation of all processes.
Why do you think product personalisation is so important right now?
Rossum Integration (Technology supplier): Because of the market situation!
ZOVOS-EKO s.r.o. (Manufacturing company): Yes, essentially the market requires it.
Studio Libertiny s.r.o (Artist): Exactly. You can think of it in terms of bigger things, but essentially it is that. It’s a precipitation of all the things that happen that come together to mean that suddenly market requires it; you can analyse it sociologically, historically, etc. From a more philosophical perspective, there is a more moving in the direction of sustainability, environment, and so on. The big topic now is on waste, as current production methods are based on the multiplication of the same thing over and over again. Even if it doesn’t sell, you produce a lot of waste. With personalisation or customisation, a lot of products can be made to measure and made to order. Unfortunately often people can’t afford this and they go to create more generic products, producing a lot of waste: fashion industry products, daily products, and so on. It’s a big issue and I think personalisation is a relatively small solution in the right direction.
Is creativity a fundamental element when it comes to generating new ways of cutting out processing?
Studio Libertiny s.r.o (Artist): Yes, but experience is just as important, because you can have creativity that is uninformed and that’s just shooting in the dark. Without experience and know-how, you can’t use creativity to its full potential.
ZOVOS-EKO s.r.o. (Manufacturing company): If I can add something to that, I think that creativity is not so important when creating processes. I think more the more important aspect, as I mentioned before, is experience, logic and understanding the bigger picture, or let’s call it the understanding of the connections in between these elements. You have to have your logical head, in my opinion, to create process. You have to put together the small pieces to generate big ones. You have to think about all the side effects, primary effects, etc.
How are lean agile manufacturing methods changing product creation?
Rossum Integration (Technology supplier): Well, I can answer this question building on what I said at the beginning, which is that our company is very customised to the customer’s needs in our main product, the container. So, in this particular case, we cannot use these lean methods.
ZOVOS-EKO s.r.o. (Manufacturing company): The lean method can be used only for mass production, not if you have a customized product. Basically every second shipping container is different. So you cannot use lean production in this case.
Rossum Integration (Technology supplier): But only in the case, for example, of the production of doors or the production of another element or another part. What we will know after the end of this project is that some parts of our main product may be possible via lean production or lean methods. I can say that we have big expectations that this will save us a lot of money in production because of increased productivity, the material that we can spare, and labour costs.
ZOVOS-EKO s.r.o. (Manufacturing company): And warehouse costs, especially if you know in advance what you need. If you can plan your production accordingly, this decreases your cost.
When moving from manual towards semi- or fully automated robotic welding fabrication, how much does the level of productivity increase?
Rossum Integration (Technology supplier): I think we set our expectations as about 20- 30%. But that said, we cannot define any further, at this stage.
ZOVOS-EKO s.r.o. (Manufacturing company): I just want to add to this that now when they are producing the doors, they basically need multiple people taking part in the process. When you introduce the welding robot, you just can keep the operator, who is a basic operator without any knowledge of welding, and even move them to a more creative position.
I can say that we have big expectations that this will save us a lot of money in production because of increased productivity, the material that we can spare, and labour costs.
Rossum Integration (Technology supplier)
Why do you think that there are certain sectors that take longer to modernize?
ZOVOS-EKO s.r.o. (Manufacturing company): Technology is not there yet. For example, virtual reality is here, but the costs are too high for certain regions to use it. It’s not applicable in reality. It’s still not at such a level that it could be used with cost in mind. A the bigger issue is that we simply don’t have enough programmers. We simply don’t have enough young people going into technical universities or technical education. Everybody wants to have simple work. To be a programmer or a specific robot one, you need to think two or three steps ahead. If you don’t think it through, you can crash the robot and cause serious damage. You have to be really strongly resistant to stress.
What are the economical, technical and societal impacts that you are expecting from the project?
Rossum Integration (Technology supplier): We’ll reduce the cost of these processes overall for people.
Studio Libertiny s.r.o (Artist): Firstly, it’ll offer a safer environment for the workers, because the dirty work will be carried out by the robotic system. There will be a positive impact on health, saving workers from related health issues. Additionally, it will reduce the costs in terms of materials and energy, which is indirectly or directly linked to the environment, and so better environment, equals better social impact, etc.
In the case of workers, how are you making the concept of working alongside robots more attractive for them?
ZOVOS-EKO s.r.o. (Manufacturing company): I would like to answer what our experience is. People are, first of all, firstly resilient about robots. Usually after three or four years, this changes and people realise that they have more time to do their job better. This is in 90% of the cases actually. First we come with a face that shows resistance towards the new technology, and then after some time they will understand that the robot is helping them. Additionally, often people assume that they will be fired, but from our experience the company is not interested in losing employees with knowledge of the functioning of the company, they just switch positions. But as I mentioned, people need time to understand what the advantages of using robots.
Building on that, how will you attract new workers, who may be resilient to taking a new job that involves collaborating with robots?
ZOVOS-EKO s.r.o. (Manufacturing company): I can speak from experience here; in one instance, we had a really dull old factory floor and we introduced ten robotic cells in one row. Now, that concrete warehouse is the ‘crown jewel’ internationally, and is an example of how we are not afraid to try something and innovating, which is in turn attractive for new engineers.
If you’d like to learn more about WRC and their experiment, don’t forget you can check out their KTE page here, including a cool video!