ODC 3D: Optimization of Digital Craftmanship in 3D Printing
Manufacturing company
The New Raw
Netherlands
Artist
Gareth Neal
United Kingdom
Technology Provider
Artific Intelligence
Findland
Background
TNR (The New Raw) is a dutch furniture manufacturer that is working towards pushing the boundaries of sustainable design in terms of material use, design & production methodology. The company employs large scale robotic 3D printing in order to process plastic waste and produce in a mass customization approach. Hence, it is possible to keep the industrial standards in quality combined with digital craftsmanship techniques, which make TNR products outstanding and unique.
The use of non standard and challenging types of plastic waste makes the 3D printing process risky. TNR succeeds in doing this through taylor-made hardware and an in-house slicing process, and manages to recycle its production waste in house and use it as filler for future productions or as material for new products.
The management and re-processing of production waste or prototyping tests adds additional costs to the operations. Moreover, the unpredictability of the prototyping of new custom and innovative shapes and objects, increases the leading time of the final production and obstructs a 24/7 operation of the facilities, thus limiting the possibilities to withstand the competition.
In this experiment, TNR will be working with artist Gareth Neal (UK), and technical partner Artific Intelligence (Finland).
Gareth Neal is a progressive and collaborative East London design and craft studio. Their work harmoniously unites traditional and digital techniques to create uniquely crafted pieces.
Artific Intelligence helps companies to explore the power of AI to benefit people and society. Their team designs and builds tailor-made and fully-automated software, drawing on machine learning, data analytics and visualisation, and AI.
Challenges
ODC 3D aims at demonstrating how craftsmanship and artificial intelligence can work together to improve the energy efficiency and optimise the fabrication of custom products made with large-scale 3D printing and recycled plastic. The project challenges are described in the figure below.
Expected impact
In terms of business impact, the improvement of the existing technologies in TNR is expected to:
- significantly increase the capacity of the company’s facilities up to 400% and produce furniture of 24 tonnes and €480K per month.
- lower the production costs per 20-30%, and making circular furniture more affordable
- reduce up to 35% of the production waste of the fabrication
Definitely, more products made out of recycled plastic waste, through more energy efficient production and resulting in less production waste will be followed by a significant environmental impact that will be seen in the reduction of plastic waste in the coastal areas and the urban centers.
Download our Factsheets
Find out more about the results and outputs of our KTEs, via these easy-to-use PDF factsheets.
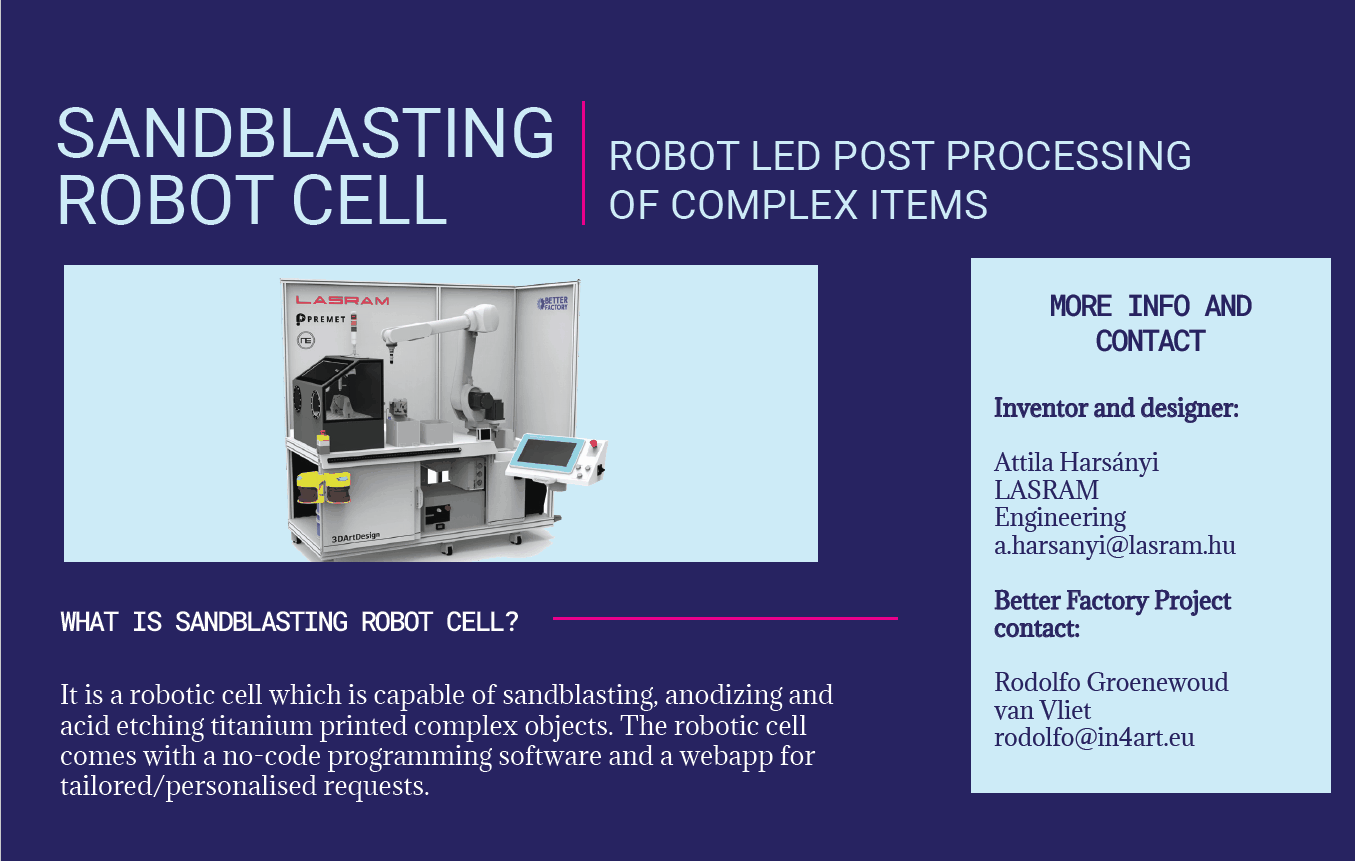